Recently, I completed a metal 3D-printing project for a customer at Terrapin Works. Terrapin Works is a laboratory at the University of Maryland that specializes in advanced additive manufacturing. I am currently a lab coordinator working at Terrapin Works, and I have had the opportunity to train on some industrial machines. One such machine is the Desktop Metal Shop System, which prints stainless steel. This is particularly useful for a customer, who is a local mechanic, that came to us with a pair of vintage motorcycle parts from the 1970's that he needed multiple copies of. The steel parts are no longer manufactured, so remodeling them in software and 3D-printing replicas was the cheapest, and most effective option for him. While I do not have an image of the original parts, the replicated models displayed below are nearly identical. Helping this mechanic is not only supporting the local community of College Park, it is also supporting an entire community of motorcycle enthusiasts. Owners of antique bikes can never find replacement parts, but with my help, they can come one step closer to a full restoration.
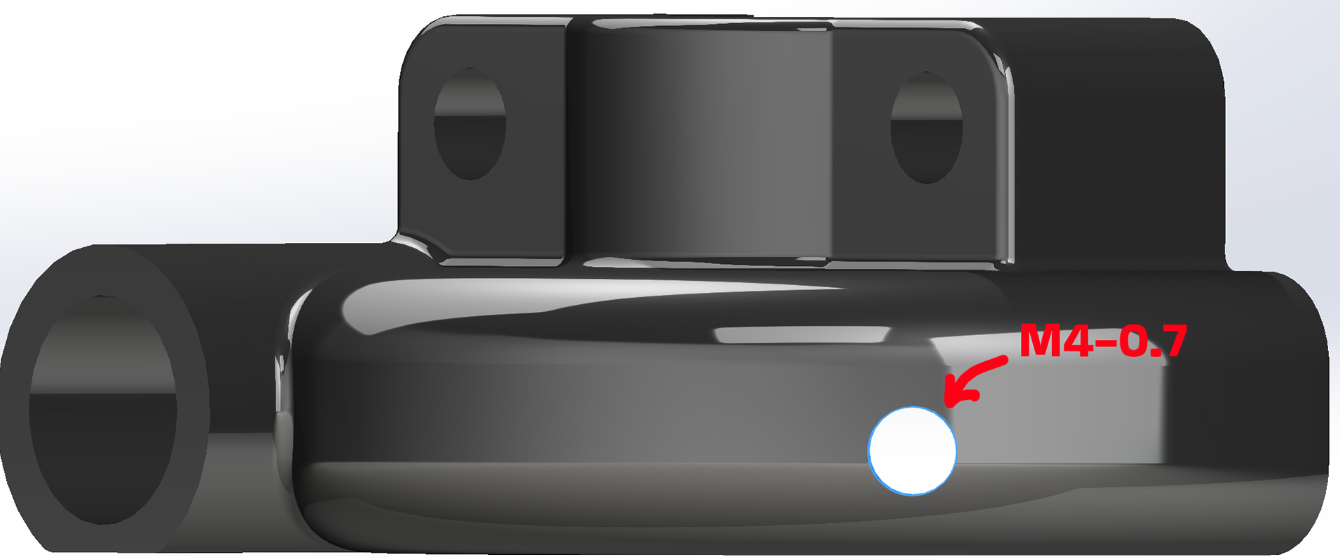
Governor hole size requirements
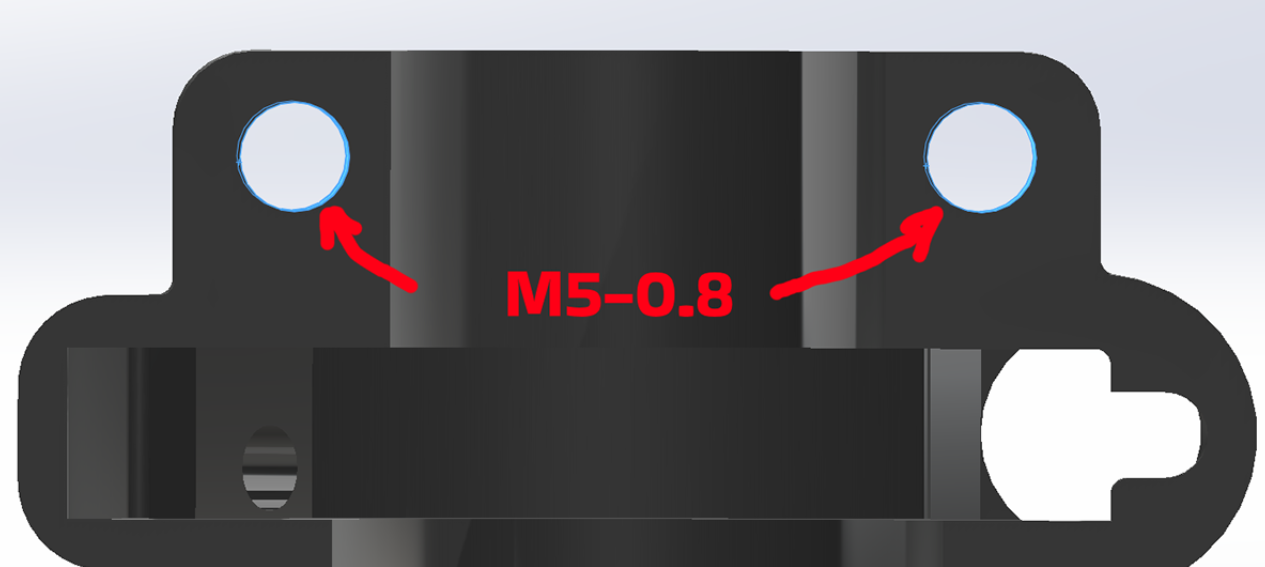
mounting hole size requirements
This project spanned 8 months and introduced me to a handful of manufacturing techniques. I started work in SolidWorks, a CAD software used for creating 3D parts, modelling the parts and a support structure by measuring the originals. Once a rough prototype was developed, I printed them out in plastic to verify the dimensions. This step was important because there were very specific requirements for some of the holes and other features on the part. Once the customer was satisfied with the plastic model, I printed the first iteration on the Desktop Metal. We anticipated some discrepancies due to the sintering process, so I used a 3D scanner to generate another model on the computer that we could compare to my original replication. Using the 3D scanner helped me find inaccurate dimensions easily, which I could correct before moving onto production. We successfully completed the first production run of 14 pairs with plans to complete another 18 pairs soon.
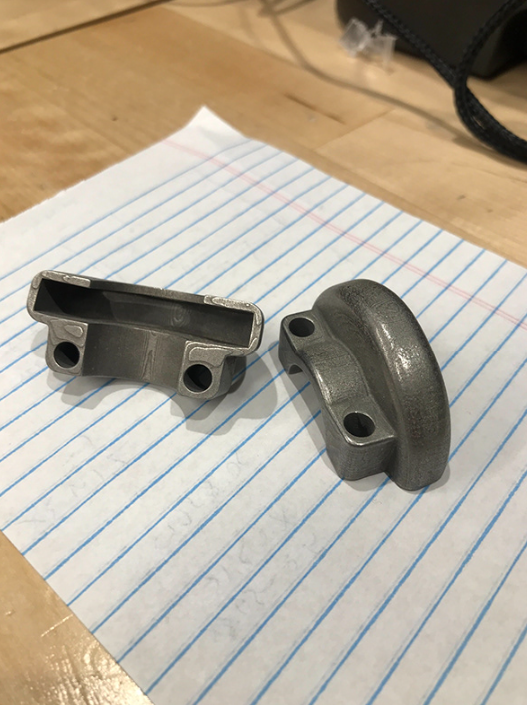
First test print
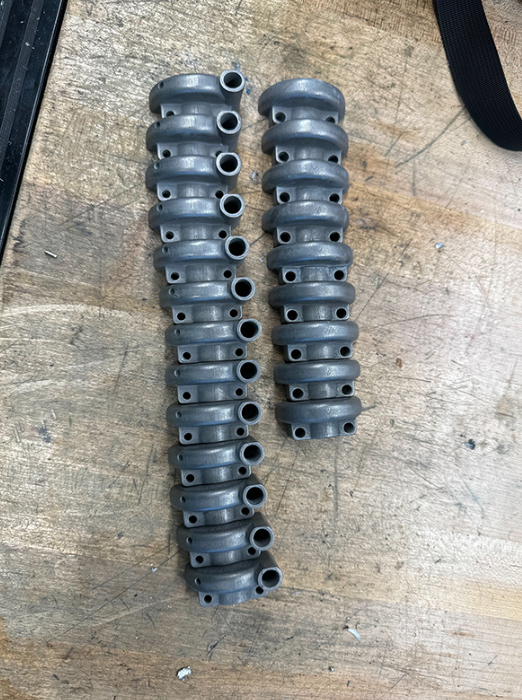
First production run
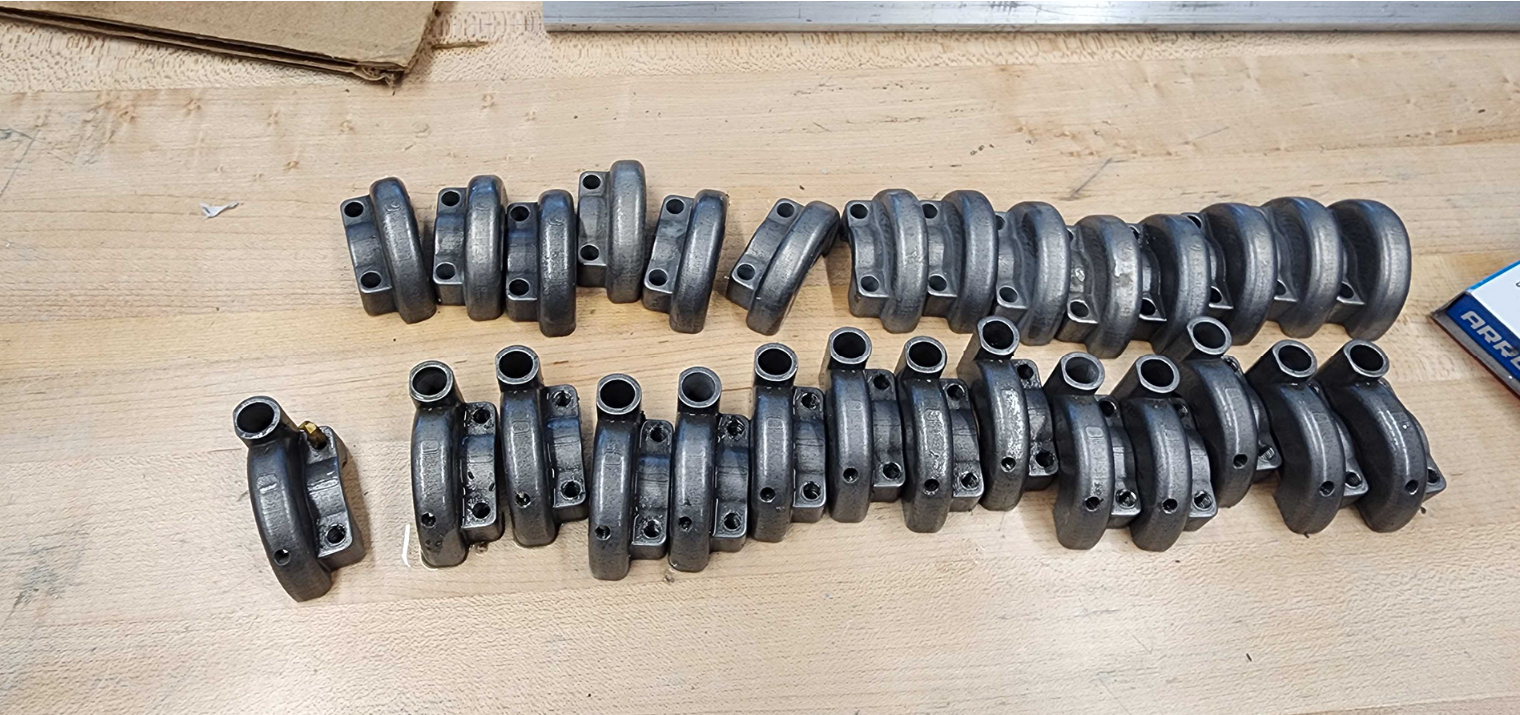
14 fully processed pairs
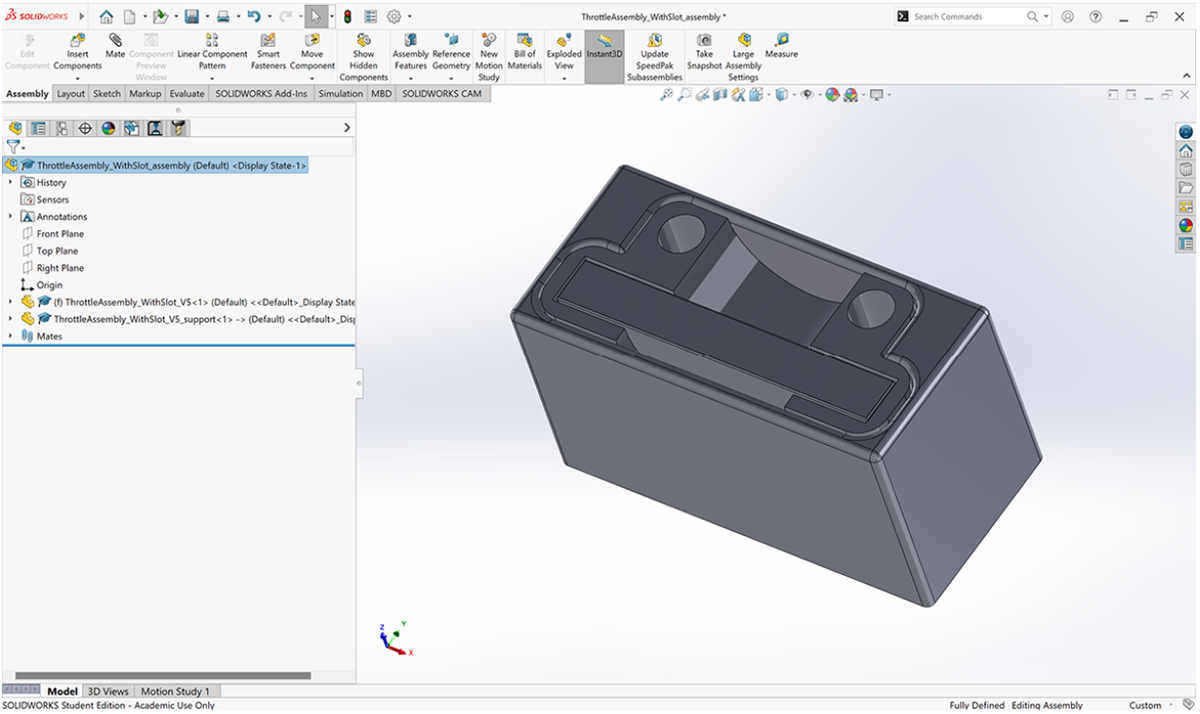
CAD assembly of the support structures

Printing the plastic test parts
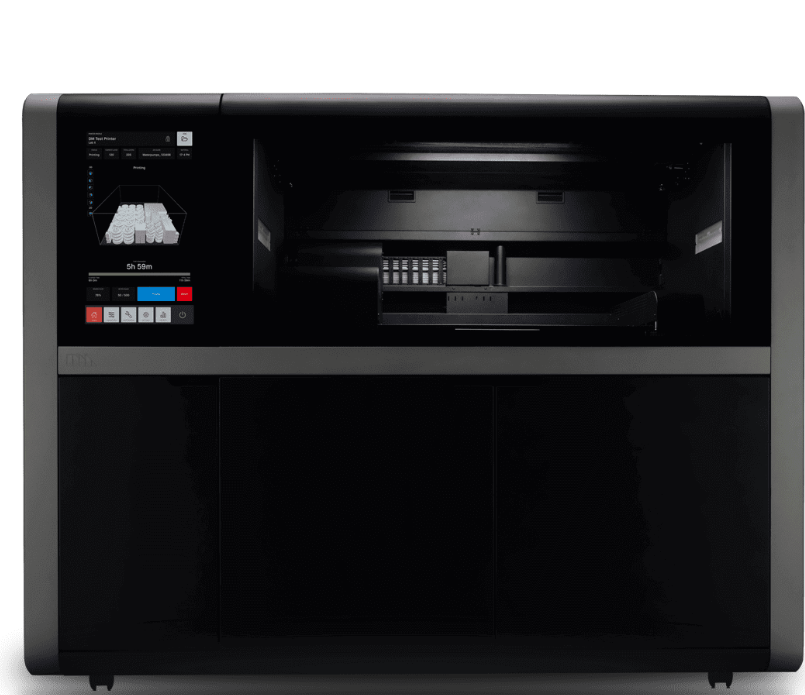